¿Qué es PCB Cerámica?
¿Qué es PCB cerámica?
Placa PCB de cerámica también se llama sustrato cerámico o placa de circuito de cerámica, placa recubierta de cobre de cerámica, sustrato cerámico se refiere a la lámina de cobre directamente unida a la alúmina (Al2O3) o nitruro de aluminio (AlN) sustrato cerámico u otra superficie de sustrato cerámico (simple o doble) en la placa de proceso especial.
PCB cerámica puede describirse como un aglutinante orgánico y polvo cerámico que conduce el calor. La conductividad térmica con la que se prepara este PCB oscila entre 9 y 20W/m.
Para explicarlo mejor, los PCB cerámicos son circuitos impresos cuyo material base es la cerámica. Este material base es altamente conductor térmico como el nitruro de aluminio, la alúmina y el óxido de berilio. Estos son muy eficaces en la transferencia de calor de los puntos calientes y luego disipar este calor sobre toda la superficie.
Además, la fabricación de PCB de cerámica se realiza con la tecnología LAM. Esta tecnología es un tipo de metalización de activación rápida por láser. Por lo tanto, los PCB cerámicos son muy versátiles y pueden sustituir fácilmente a todos los PCB tradicionales. Este PCB lo conseguirá con un rendimiento aún mayor y con una construcción menos complicada.
1. La diferencia entre el sustrato cerámico y la placa PCB
Sustrato de cerámica es que decimos placa de circuito de cerámica, PCB de cerámica y placa de circuito impreso tienen la misma interconexión de circuitos, a través de características de conducción de agujero. Entonces, ¿cuáles son las diferencias entre el sustrato cerámico y placa de PCB?
(1)La conductividad térmica de la placa PCB y el sustrato cerámico es diferente
El sustrato cerámico está hecho de sustrato cerámico, es decir, el medio es material cerámico, incluyendo base cerámica de alúmina, base cerámica de nitruro de aluminio, base cerámica de nitruro de silicio, el rendimiento de disipación de calor de cerámica es muy bueno, la conductividad térmica del sustrato cerámico de 25w a 230w, la conductividad térmica del medio cerámico es diferente. La conductividad térmica del sustrato cerámico de alúmina es de 25w~30w, la conductividad térmica del sustrato cerámico de nitruro de aluminio es superior a 170w, y la conductividad térmica del sustrato cerámico de nitruro de silicio es de 80w~90w. A continuación, la placa PCB es por lo general el uso de medio es fr4 o sustrato metálico, la conductividad térmica es inferior a 3w, y la brecha es demasiado grande en comparación con sustrato cerámico, especialmente la necesidad de un alto rendimiento de disipación de calor del campo de productos, sustrato cerámico se ha convertido en un material muy popular medio.
(2)El aislamiento del sustrato cerámico y de la placa PCB es diferente
Sustrato de cerámica es generalmente la línea de capa - base de cerámica - estructura de la capa de línea, el aislamiento de sustrato de cerámica es muy bueno, también está determinada por el material cerámico en sí, no hay necesidad de añadir capa de aislamiento. tablero de PCB tiene que añadir una capa aislante para desempeñar un papel de aislamiento móvil, pero el efecto de aislamiento es mucho menor que el sustrato de cerámica.
(3) La estructura de disipación de calor del sustrato cerámico es diferente de la de PCB
La estructura de disipación de calor del sustrato cerámico es la estructura de la capa de circuito - base cerámica - capa de placa de circuito. Debido a que no hay capa aislante en el medio, el calor del dispositivo se transfiere directamente desde la base de cerámica a la capa de circuito y la disipación de calor está fuera, la disipación de calor es rápida y el efecto es bueno. tablero de PCB es la necesidad de calor de la capa media - capa aislante - capa de línea, separados por una capa aislante, al mismo tiempo, la capa dieléctrica en sí de la conductividad térmica es pobre, a continuación, añadir adhesivo de conducción de calor, el efecto de conducción de calor aún no se ha mejorado, a menudo no puede lograr el propósito de dispositivo de disipación de calor rápida. En particular, algunos dispositivos de alta potencia necesitan utilizar sustrato cerámico como sustrato de refrigeración en el campo de productos donde la disipación de calor y el cambio de temperatura es relativamente grande.
(4) La aplicación del sustrato cerámico y la placa PCB es diferente
El sustrato cerámico y la aplicación de la placa PCB es diferente, principalmente el rendimiento de los dos es diferente, el sustrato cerámico se utiliza en alta conductividad térmica, alta disipación de calor, alto aislamiento, campo de productos, tales como iluminación LED de alta potencia, módulo de alta potencia, comunicación de alta frecuencia, fuente de alimentación de pista; La placa PCB ordinaria se utiliza en algunos más extensos, disipación de calor, aislamiento y otros requisitos no son estrictos, utilizados en productos comerciales privados.
(5) El precio del sustrato cerámico es diferente al de la placa PCB
El material y el rendimiento del sustrato de cerámica y la placa de PCB son diferentes, y la decisión final es que sus precios son diferentes. La placa de sustrato cerámico es muy alta y el coste de producción es elevado.
El sustrato cerámico tiene grandes ventajas, pero el sustrato cerámico es frágil y tiene un alto índice de desechos, lo que requiere un alto nivel de tecnología de producción. Sin embargo, no se puede hacer una placa de circuito con el tamaño de más de un metro como las placas de PCB ordinarias. Hitech Circuits tiene más de 10 años de experiencia en la industria de placas de circuito de cerámica, y muchas universidades e instituciones de I + D están en la cooperación, la bienvenida a la investigación.
2.Diferencia entre el sustrato cerámico y la placa de alta frecuencia
El material es diferente. El sustrato cerámico está hecho de óxido de aluminio o nitruro de aluminio, y la placa de alta frecuencia está hecha de Rogers, Yaron, PTFE, etc., con baja constante dieléctrica y alta velocidad de comunicación de frecuencia.
El rendimiento es diferente. El sustrato cerámico se utiliza ampliamente en refrigeración y sistemas, módulos de alta potencia, electrónica del automóvil y otros campos. La placa de alta frecuencia se utiliza principalmente en el campo de la comunicación de alta frecuencia, la aviación, la electrónica de consumo de gama alta, etc. Campo de la comunicación de alta frecuencia implica requisitos de disipación de calor, por lo general necesitan ser combinados con la base de cerámica y placa de alta frecuencia, tales como PCB de cerámica de alta frecuencia.
1. Aplicación del sustrato cerámico
Los sustratos cerámicos se utilizan en chips led para conseguir una mejor conductividad térmica. Además, el sustrato cerámico también se utiliza para fabricar chips cerámicos en los siguientes dispositivos electrónicos:
◆Módulo semiconductor de alta potencia.
◆Enfriador de semiconductores, calentador electrónico; Circuito de control de potencia, circuito de mezcla de potencia.
◆Módulo de potencia inteligente; Fuente de alimentación conmutada de alta frecuencia, relé de estado sólido.
◆Componentes electrónicos de automoción, aeroespaciales y militares.
◆Módulo de panel solar; Central privada de telecomunicaciones, sistema receptor; Láser y otros componentes electrónicos industriales.
Aplicación del sustrato cerámico en semiconductores de tercera generación
Los dispositivos de potencia de corriente principal representados por MOSFET, IGBT y transistor ocupan un lugar en sus propios segmentos de frecuencia y fuente de alimentación. Debido al excelente rendimiento integral de IGBT, ha sustituido a GTR, convertido en el inversor, UPS, convertidor de frecuencia, accionamiento del motor, fuente de alimentación de conmutación de alta potencia, especialmente ahora el vehículo eléctrico caliente, ferrocarril de alta velocidad y otros dispositivos electrónicos de potencia en los dispositivos de corriente principal.
Aplicación del sustrato cerámico de alúmina en el campo de la electrónica de potencia
En el campo de la electrónica de potencia, como la fuente de alimentación de conmutación de potencia, el accionamiento eléctrico, etc., el sustrato cerámico dieléctrico es necesario para lograr una mejor conductividad térmica, evitar la quema de corriente y el cortocircuito.
Aplicación de la placa de cerámica de alúmina cocida en la industria de las baterías de litio
Con la recomendación de la inteligencia artificial y la protección del medio ambiente, la industria del automóvil también ha lanzado coches eléctricos, principalmente a través del almacenamiento de baterías. Las baterías de litio fabricadas con sustrato cerámico pueden lograr mejores funciones de disipación de corriente y calor, promoviendo la demanda del mercado de vehículos de nueva energía.
2. Ventajas del sustrato cerámico
A. El coeficiente de expansión térmica del sustrato cerámico es cercano al del chip de silicio, lo que puede ahorrar la lámina Mo de la capa de transición, ahorrar mano de obra, ahorrar material y reducir costes;
B. Reduce la capa de soldadura, reduce la resistencia térmica, reduce la cavidad;
C. Bajo el mismo flujo de carga, la anchura del alambre de la lámina de cobre de 0,3 mm de espesor es sólo el 10% de la de la placa de circuito impreso ordinaria;
D. Excelente conductividad térmica, por lo que el embalaje del chip es muy compacto, por lo que la densidad de potencia se incrementa en gran medida, mejorar la fiabilidad del sistema y el dispositivo;
E. El sustrato cerámico ultrafino (0,25 mm) puede sustituir al BeO, sin problemas de toxicidad medioambiental;
F. Gran capacidad de carga, 100A de corriente continua a través de un cuerpo de cobre de 1mm de ancho y 0,3mm de espesor, el aumento de temperatura es de unos 17℃; Con 100A de corriente continua pasando a través de un cuerpo de cobre de 2mm de ancho y 0,3mm de espesor, el aumento de temperatura es sólo de unos 5℃.
G. Baja resistencia térmica, 10×10mm sustrato cerámico 'resistencia térmica de 0,63mm de espesor de sustrato cerámico es de 0,31K/W, 0,38mm de espesor de sustrato cerámico es de 0,19K/W, 0,25mm de espesor de sustrato cerámico es de 0,14K/W.
H. Alto aislamiento y alta resistencia a la presión para garantizar la seguridad personal y la protección del equipo.
I. Se pueden realizar nuevos métodos de embalaje y ensamblaje, por lo que el producto está muy integrado y el tamaño es reducido.
3. Tecnología de sustratos cerámicos
En la actualidad, los tipos comunes de sustrato cerámico de disipación de calor incluyen HTCC, LTCC, DBC y DPC. DBC y DPC para el doméstico en los últimos años para desarrollar maduro, y la producción de energía de la tecnología profesional, DBC es el uso de calentamiento a alta temperatura Al2O3 y Cu combinación de placa, su cuello de botella técnica no es fácil de resolver el problema de los microporos entre Al2O3 y Cu placa, lo que hace que la energía de producción en masa y el rendimiento del producto por el mayor desafío. La tecnología DPC es el uso de la tecnología de cobreado directo, la deposición de Cu sobre el sustrato de Al2O3, su proceso combinado con el material y la tecnología de la película, su producto es el sustrato de refrigeración de cerámica más utilizado en los últimos años. Sin embargo, su control de materiales y los requisitos de capacidad de integración de la tecnología de proceso son altos, lo que hace que el umbral técnico para entrar en la industria DPC y la producción estable sea relativamente alto.
(1) HTCC (cerámica de cocción a alta temperatura)
El proceso de fabricación de la HTCC es muy similar al de la LTCC. La principal diferencia es que al polvo cerámico de HTCC no se le añade material de vidrio. Por lo tanto, el polvo cerámico de HTCC debe secarse y endurecerse en forma embrionaria a una alta temperatura de 1300~1600℃. Debido a su alta temperatura de cocción, la elección de los materiales conductores de metal es limitada, sus principales materiales de alto punto de fusión, pero pobre conductividad de tungsteno, molibdeno, manganeso ... como el metal, y finalmente el moldeo por sinterización laminar.
(2) LTCC (cerámica de cocción a baja temperatura)
El LTCC también se conoce como sustrato cerámico multicapa de cocción a baja temperatura. En esta tecnología, el polvo inorgánico de óxido de aluminio y alrededor del 30%~50% de material de vidrio se combinan con aglutinante orgánico para que se mezcle uniformemente en una lechada de lodo. A continuación, el lodo se raspa en láminas con un rascador y, mediante un proceso de secado, el lodo en láminas se convierte en una fina pieza en bruto. Como la transmisión de señales a todos los niveles.
Para las líneas internas de LTCC, se utiliza la tecnología de serigrafía para rellenar agujeros e imprimir líneas en los embriones en bruto, y los electrodos internos y externos pueden ser de plata, cobre, oro y otros metales, respectivamente. Por último, las capas se apilan y sinterizan en el horno de sinterización a 850~900℃.
(3) Cobre de unión directa (DBC)
La tecnología de recubrimiento directo de cobre es el uso de líquido eutéctico de oxígeno de cobre directamente sobre el recubrimiento cerámico, el principio básico es introducir una cantidad apropiada de oxígeno entre el cobre y la cerámica antes o durante el proceso de recubrimiento, en el rango de 1065℃~1083℃, el cobre y el oxígeno forman el líquido eutéctico Cu-O, la tecnología DBC utiliza la solución eutéctica para reaccionar químicamente con el sustrato cerámico y formar la fase CuAlO2 o CuAl2O4, por un lado, y para infiltrarse en la lámina de cobre y realizar la combinación del sustrato cerámico y la placa de cobre, por otro.
(3) DPC (Cobre de placa directa)
DPC también se conoce como sustrato de cobreado directo. Tomemos como ejemplo el proceso de sustrato DPC: En primer lugar, el sustrato cerámico se trata previamente y se limpia, y el sustrato cerámico se pulveriza sobre el sustrato cerámico y se combina con la capa de compuesto de cobre mediante el uso de la tecnología de recubrimiento al vacío de fabricación de película delgada. A continuación, se realiza el circuito mediante el proceso de reexposición, revelado, grabado y eliminación de la película con la fotorresistencia de microsombra de luz amarilla. Por último, se aumenta el grosor del circuito mediante deposición galvanoplastia/electrodeposición sin galvanoplastia, y se fabrica el circuito metalizado después de eliminar la fotorresistencia.
3. Proceso de producción del sustrato cerámico
1. Perforación
El sustrato cerámico se utiliza generalmente por perforación láser, en comparación con la tecnología de perforación tradicional, la tecnología de perforación láser tiene las ventajas de alta precisión, velocidad rápida, alta eficiencia, perforación masiva a gran escala, adecuado para la gran mayoría de materiales duros y blandos, sin pérdida de herramientas, en línea con la interconexión de alta densidad de placa de circuito impreso, desarrollo fino.
A través del proceso de perforación láser de sustrato cerámico tiene alta fuerza de unión de cerámica y metal, no se caiga, fenómeno de formación de espuma, para lograr el efecto de crecimiento juntos, alta suavidad de la superficie, la rugosidad en 0,1μm ~ 0,3μm, la apertura de perforación láser en 0,15 mm-0,5 mm, incluso puede llegar a 0,06 mm.
2、Recubrimiento de cobre
El revestimiento de cobre se refiere al área sin cableado en la placa de circuito cubierta con lámina de cobre, conectada con el cable de tierra, con el fin de aumentar el área de cable de tierra, reducir el área de bucle, reducir la caída de tensión, mejorar la eficiencia energética y la capacidad antiinterferente. El revestimiento de cobre no sólo puede reducir la impedancia de tierra, sino también reducir el área de la sección transversal del bucle y mejorar el bucle de espejo de la señal. Por lo tanto, el proceso de recubrimiento de cobre juega un papel muy importante en el proceso de PCB de sustrato cerámico, incompleto, truncado bucle de espejo o posición incorrecta de la capa de cobre a menudo conducen a nuevas interferencias, tienen un impacto negativo en el uso de la placa.
3. Grabado
Los sustratos cerámicos también necesitan ser grabados, con el patrón del circuito pre-recubierto con una capa de resistencia de plomo-estaño, y luego químicamente grabado el cobre desprotegido, no conductor para formar el circuito. El grabado se divide en grabado de la capa interna y grabado de la capa externa, el grabado de la capa interna se realiza con ácido, con película húmeda o película seca como resistencia a la corrosión; el grabado externo es alcalino con estaño y plomo como resistencia.
Hay muchos tipos de procesos de fabricación de productos cerámicos en la fábrica de placas de circuitos. Se dice que hay más de 30 tipos de procesos de fabricación, tales como prensado en seco, lechada, extrusión, inyección, fundición y prensado isostático. Debido a que el sustrato cerámico electrónico es de tipo "plano", la forma no es complicada, el proceso de fabricación de conformado en seco y procesamiento es simple y el coste es bajo, por lo que la mayoría de ellos utilizan el método de conformado de prensado en seco. El proceso de fabricación de la cerámica electrónica PCB de prensado en seco incluye principalmente la formación de la pieza en bruto, la sinterización de la pieza en bruto y el acabado, formando el circuito en el sustrato.
1. Fabricación ecológica del sustrato cerámico (conformado)
Utilice polvo de alúmina de alta pureza (contenido ≥95% Al2O3) (se requieren diferentes tamaños de partícula dependiendo del propósito y el método de fabricación. Por ejemplo, desde unos pocos analitos hasta decenas de micras) y aditivos (principalmente adhesivos, dispersantes, etc.). Forman una "pasta" o material procesado.
(1) Prensado en seco de sustrato cerámico para producir piezas verdes (o "verdes").
Tocho de prensado en seco es el uso de alúmina de alta pureza (cerámica electrónica con contenido de alúmina superior al 92%, la mayor parte del uso de 99%) en polvo (partículas de prensado en seco no excederá de 60μm, para la extrusión, laminación, inyección y otras partículas de polvo deben ser controlados dentro de 1μm) añadir la cantidad adecuada de plastificante y aglutinante, mezclado uniformemente después de tocho de prensado en seco. En la actualidad, la descendencia de piezas cuadradas o redondas puede alcanzar 0,50 mm, o incluso ≤0,3 mm (dependiendo del tamaño de la placa). Los tochos prensados en seco pueden procesarse antes de la sinterización, como el dimensionado y el taladrado. Mecanizado, pero tenga cuidado de compensar la contracción de tamaño causada por la sinterización (aumentar el tamaño de la contracción).
(2) Producción de tocho verde por el método de esparcimiento de sustrato cerámico.
Líquido de cola de flujo (polvo de óxido de aluminio + disolvente + dispersante + adhesivo + plastificante mezclados uniformemente + tamizado) fabricación + colada de flujo (en la máquina de colada de flujo cola sobre metal o cinta de poliéster resistente al calor) + secado + recorte (también puede ser otro procesamiento) + desengrasado + sinterización y otros procesos. Puede realizar la automatización y la producción a escala.
2. Sinterización y acabado del tocho verde después de la sinterización. Las piezas brutas de sustrato cerámico a menudo necesitan ser "sinterizadas" y acabadas después de la sinterización.
(1) Sinterización del sustrato cerámico en bruto.
Tocho de cerámica "sinterización" se refiere al proceso de "sinterización", el tocho (volumen) en la cavidad, el aire, las impurezas y la materia orgánica como la eliminación de la presión en seco, de modo que su volatilización, combustión, extrusión, y la eliminación de partículas de alúmina. Lograr el contacto cercano o proceso de crecimiento combinado, por lo que después de la sinterización de tocho de cerámica verde, habrá pérdida de peso, la contracción del tamaño, deformación de la forma, aumento de la resistencia a la compresión y la reducción de la porosidad y otros cambios.
Los métodos de sinterización de tocho de cerámica son los siguientes: ① sinterización atmosférica, sinterización sin presión traerá gran deformación; ② presión (prensado en caliente) sinterización, sinterización a presión, puede obtener buenos productos planos es el método más comúnmente utilizado; ③ sinterización isostática caliente es el uso de sinterización de gas caliente a alta presión. Sus productos característicos están acabados a la misma temperatura y presión. Todo tipo de equilibrio de rendimiento, el costo es relativamente alto. En el valor añadido de los productos, o aeroespacial, defensa nacional y productos militares en el uso de este método de sinterización, tales como el campo militar de espejos, combustible nuclear, barril y otros productos. La temperatura de sinterización de tochos verdes de alúmina prensada en seco es en su mayoría entre 1200℃ y 1600℃ (dependiendo de la composición y el flujo).
(2) Acabado del sustrato cerámico después de la sinterización (cocido) en blanco.
La mayoría de las palanquillas cerámicas sinterizadas requieren acabado. El propósito es: ① obtener una superficie plana. En el proceso de sinterización a alta temperatura de tocho verde, debido al desequilibrio de la distribución de partículas, huecos, impurezas y materia orgánica en el tocho verde, causará deformación, desnivel o excesiva rugosidad y diferencia. Estos defectos pueden solucionarse mediante el acabado superficial; ② Obtener una superficie de alto acabado, como la reflexión especular, o mejorar la lubricidad (resistencia al desgaste).
El tratamiento de pulido superficial consiste en utilizar materiales de pulido (como carburo de silicio, B4C) o pasta de arena de diamante para pulir gradualmente la superficie de abrasivo grueso a fino. En general, el uso de polvo de AlO o pasta de diamante ≤1μm, o láser o procesamiento ultrasónico para lograr.
(3) tratamiento fuerte (acero).
¡Después de pulir la superficie, con el fin de mejorar la resistencia mecánica (como la resistencia a la flexión, etc.), recubrimiento de vacío de rayos electrónicos, recubrimiento de vacío de pulverización catódica, evaporación química de vapor y otros métodos se pueden utilizar para chapar una capa de película de compuesto de silicio, a través de 1200℃ ~ 1600℃ tratamiento térmico, puede mejorar significativamente la resistencia mecánica de piezas de cerámica!
3. Formar un patrón conductor (circuito) en el sustrato.
Para procesar gráficos conductores (circuitos) en sustratos cerámicos, es necesario fabricar primero sustratos cerámicos recubiertos de cobre y, a continuación, fabricar placas de circuito impreso cerámicas de acuerdo con la tecnología PCB.
(1) Formación de un sustrato cerámico recubierto de cobre. Actualmente existen dos métodos para formar sustratos cerámicos recubiertos de cobre.
① Método de laminación. Se forma prensando en caliente una cara de lámina de cobre oxidada y sustrato cerámico de alúmina. Es decir, la superficie cerámica es tratada (como láser, plasma, etc.), obtener superficie activada o rugosa, y luego de acuerdo con la "lámina de cobre + capa aglutinante resistente al calor + cerámica + capa aglutinante resistente al calor + lámina de cobre" laminar juntos, después de 1020℃ ~ 1060℃ sinterización, la formación de doble cara laminado cerámico recubierto de cobre. ② Método de galvanoplastia. Después del tratamiento con plasma, el sustrato cerámico es "sputtered película de titanio + sputtered película de níquel + sputtered película de cobre", y luego galvanoplastia convencional de cobre hasta el espesor de cobre requerido, es decir, la formación de sustrato cerámico recubierto de cobre de doble cara.
(2) Fabricación de placas PCB de cerámica de una y dos caras. De acuerdo con las técnicas tradicionales de fabricación de PCB, se utilizan sustratos cerámicos recubiertos de cobre de una y dos caras.
(3) Fabricación de placas cerámicas multicapa.
① En paneles simples y dobles recubiertos repetidamente capa de aislamiento (alúmina), sinterización, cableado, sinterización para formar placa multicapa de PCB, o el uso de la tecnología de fabricación de fundición para completar. ② Placa multicapa de cerámica se fabrica por el método de fundición. La cinta en bruto se forma en la máquina de fundición, a continuación, perforación, taponamiento (pegamento conductor, etc.), impresión (circuito conductor, etc.), corte, laminación, prensado isostático para formar placa multicapa de cerámica. Hitech Circuits tiene más de 10 años de experiencia en la fabricación de sustratos cerámicos, así que no dude en consultarles si necesita saber más cuestiones técnicas.
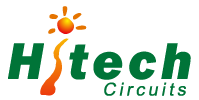
+86-755-29970700 or +86-(0)133 1684 4961
sales@hitechpcb.com; sales15@hitechcircuits.com
2F, Building C, Suojia Technology Park, Hangcheng, Bao’an, Shenzhen, Guangdong, China 518126