Proceso de Ensamblaje de PCB
Proceso de Ensamblaje de PCB
En primer lugar, le llevará a conocer una breve historia del desarrollo de PCBA, también llamado ensamblaje de PCB. PCBA es la abreviatura, lo que significa que el proceso de SMT de la PCB terminado o el proceso de pasar por el DIP o THT. Entonces se abrevia como PCBA. De hecho, se conoce comúnmente como placa electrónica o placa de circuito.
Placa de circuito, abreviado como PCB, es un componente electrónico importante y el apoyo de los componentes electrónicos. Esta es la versión más antigua. Más tarde, los austriacos crearon nuevas tecnologías que eliminaron los metales no deseados y añadieron cableado, formando la versión que utilizamos actualmente.
Debido a su posición en la última mitad del proceso de los equipos electrónicos, la PCBA se conoce como la fase posterior de la industria electrónica. Dado que todos los dispositivos y equipos electrónicos requieren el soporte de PCBA, este proyecto tiene la mayor parte del mercado electrónico. En la actualidad, existen enormes áreas industriales en todo el mundo que fabrican placas de circuito impreso (PCB).
Los ordenadores y productos relacionados, los dispositivos de comunicación y los aparatos electrónicos son los principales grupos consumidores de PCBA. Entre ellos se encuentran habitualmente los ordenadores utilizados en el hogar, televisores, luces LED, teléfonos móviles, tabletas, etc. Debido a que todos los hogares lo utilizan, el desarrollo económico de PCBA es rápido y se ha convertido rápidamente en el primero del mundo.
PCBA sigue desarrollándose, y para hacer la vida de la gente más conveniente, hay varias condiciones generales para su desarrollo:
a. Desarrollar enérgicamente la IDH para que PCBA sean más precisos y pequeños.
b. PCBA también necesita asegurar una fuerte vitalidad y vida útil para durar más tiempo.
c. Actualizar el equipo de producción y el proceso de fabricación.
En el procesamiento de PCBA, se utilizan componentes SMD y componentes enchufables (THT, Through-hole technology).
Capítulo 1: Componentes SMD y componentes enchufables (THT)
¿Cuál es la diferencia entre los componentes SMD y los componentes enchufables (THT)?
1、 Las diferencias entre ambos son las siguientes:
1.1 Los componentes SMD son más pequeños, ligeros y fáciles de soldar que los componentes enchufables.
1.2 Una ventaja importante de los componentes SMD es que mejoran la estabilidad y fiabilidad del circuito. Al no tener cables, los componentes SMD reducen los campos eléctricos y magnéticos parásitos, lo que resulta especialmente eficaz en circuitos analógicos de alta frecuencia y circuitos digitales de alta velocidad.
2、 Método de soldadura para ambos
2.1 Método de soldadura de componentes SMD:
Coloque el componente sobre la almohadilla de soldadura, aplique la pasta de soldadura SMD preparada sobre la superficie del componente y el área de contacto entre la almohadilla de soldadura y, a continuación, caliente la conexión entre la almohadilla de soldadura y el componente SMD con un soldador eléctrico de calentamiento interno de 20 W (la temperatura debe estar entre 220~230 ℃). Una vez fundida la soldadura, retire el soldador eléctrico y espere a que la soldadura se solidifique antes de finalizar la soldadura. Después de la soldadura, se pueden utilizar pinzas para sujetar los componentes soldados para ver si hay alguna flojedad. Si no hay holgura, significa que la soldadura es buena. Si hay holgura, vuelva a aplicar pasta de soldadura y suelde de nuevo según el método anterior.
2.2 Método para soldar componentes THT:
Al soldar todas las patillas, se añadirá soldadura a la punta del soldador y se aplicará fundente a todas las patillas para mantenerlas húmedas. Toque el extremo de cada patilla del chip con la punta del soldador hasta que la soldadura fluya dentro de las patillas. Una vez soldadas todas las patillas, humedézcalas con fundente para limpiar el estaño de soldadura, a fin de eliminar cualquier cortocircuito y solapamiento. Por último, utilice unas pinzas para comprobar si hay alguna soldadura defectuosa. Tras la inspección, retire el fundente de la placa de circuito y limpie con cuidado el cepillo duro a lo largo de la dirección de las patillas con alcohol hasta que desaparezca el fundente.
Capítulo 2: Proceso completo de PCBA
Después de aprender algo sobre los componentes, aquí tienes el proceso completo de ensamblaje de una placa PCB:
Paso 1: Aplicar pasta de soldadura a la placa PCB
En este paso, obviamente se utilizará la plantilla de acero inoxidable y la pasta de soldadura.
La pasta de soldadura debe aplicarse uniformemente a la placa de circuito impreso en los PAD correctos y en las ubicaciones necesarias.
Paso 2: Utilizar la máquina de montaje para Recoger y colocar
Los componentes montados en superficie o SMD deben colocarse en una PCB preparada mediante una máquina de montaje automatizada. A continuación, los componentes deben soldarse en los pads correctos de las placas de circuito impreso.
Paso 3: Pasar por el reflujo para soldar los componentes
Este proceso ayudará a que la pasta de soldadura se solidifique y, para adherir los componentes a la PCB, la pasta de soldadura necesita pasar por el reflujo y permanecer durante un periodo de tiempo para obtener una mejor soldadura.
Paso 4: Inspeccionar el ensamblaje de PCB semiacabado
Una vez que el proceso de reflujo ha finalizado y los componentes de montaje están soldados en el lugar correcto, llega la inspección de PCB actual durante la etapa SMT. La placa ensamblada debe probarse e inspeccionarse para comprobar su funcionalidad, por ejemplo, utilizando plantillas ICT, AOI, etc.
Entre las formas de comprobar la calidad de PCBA se incluyen las siguientes básicas:
Inspección manual: El trabajador de producción y la persona del departamento de calidad deben realizar una inspección visual para garantizar la buena calidad de PCB.
Inspección óptica automática (denominada AOI): Un método de inspección y una determinada máquina más apropiados para grandes lotes de PCBA. Una máquina de inspección óptica automática, o máquina AOI, utiliza cámaras de alta potencia, colocadas en diferentes ángulos para ver las conexiones soldadas.
Inspección por rayos X: Una máquina de inspección que se utiliza para PCB más complejas examinando las capas de la PCB e identificando problemas potenciales, especialmente para aquellas que tienen BGAs, QFNs, etc.
Paso 5: Insertar el componente de agujero pasante
Un orificio pasante chapado, o PTH, es un orificio en la PCB. Está chapado a través de la placa. En lugar de pasta de soldar, se requiere un método de soldadura más especializado para este proceso. Generalmente, después de insertar los componentes en el agujero, las placas se sueldan por ola.
Soldadura manual: para placas sencillas, a veces se puede utilizar la soldadura manual, pero no se recomienda siempre.
Soldadura por ola: La versión automatizada de la soldadura manual en la que una ola de soldadura fundida suelda todos los agujeros que requieren soldadura en la parte inferior de la placa a la vez.
Paso 6: Finalizar la inspección final
Una vez completado y finalizado todo el proceso de soldadura del ensamblaje de la PCB, es el momento de realizar una inspección final y una prueba funcional. Esto dependerá de los requisitos de cada proyecto y de cada cliente. Incluye la prueba ICT y la prueba FCT.
Ejecute señales de alimentación y simuladas para probar las características eléctricas de la placa de circuito impreso. Una señal de que la PCB ha fallado es cuando muestra la fluctuación de señales eléctricas durante la prueba.
Si la PCB falla durante la inspección final, debe volver a comprobarse y probarse. Y el proceso vuelve a empezar hasta que se produce PCB bueno y satisfactorio.
Capítulo 3: Algunas tecnologías especiales en SMT
La soldadura por reflujo se utiliza para fundir la pasta de soldadura con el fin de soldar y fijar los componentes electrónicos. La soldadura por reflujo se divide en cuatro zonas de temperatura: precalentamiento, temperatura constante, calentamiento y enfriamiento.
Cada zona de temperatura tiene funciones diferentes. La soldadura por reflujo ordinaria es principalmente la soldadura por reflujo de aire, que se ocupa de los productos electrónicos ordinarios, mientras que los productos con altos requisitos de calidad, estabilidad y tasa de vacío (como la electrónica de automoción, aviónica, electrónica médica, etc.) necesitarán soldadura por reflujo de nitrógeno, incluso soldadura por reflujo de vacío. Esto significa introducir el nitrógeno durante la soldadura por reflujo.
En la soldadura por reflujo, el nitrógeno se suele utilizar en las zonas de calentamiento y enfriamiento. ¿Por qué es necesario añadir nitrógeno? Hablemos de este tema aquí.
Hay tres razones principales para añadir nitrógeno a la soldadura por reflujo.
1. Reducir la oxidación
2. Aumentar la humectabilidad y mejorar la calidad de la soldadura
3. Reducir la fracción vacía
Los detalles son los siguientes
1. Reducir la oxidación en el horno
Debido a que el nitrógeno es un gas inerte, después de agregar nitrógeno, el fondo del reflujo es ocupado por nitrógeno, aislando el oxígeno en el fondo del reflujo, reduciendo así el contacto con el oxígeno y reduciendo la reacción de oxidación de PCBA a través del reflujo.
2. Aumenta la humectabilidad y mejora la calidad de la soldadura
El gas nitrógeno ocupa la parte inferior de la zona de temperatura de calentamiento, lo que aumenta la humectabilidad de la pasta de soldadura durante la fusión en caliente a altas temperaturas. Esto permite soldar mejor varios componentes y garantiza la mejora de la calidad de la soldadura.
3. Reducir la fracción vacía
La fracción vacía siempre ha sido un indicador técnico de la soldadura por reflujo. La razón principal para el uso de nitrógeno para reducir la tasa de vacío es que el nitrógeno es un gas inerte, que hace que los pads de PCB y los componentes aíslen en gran medida las moléculas de oxígeno y vapor de agua en el aire, y acelera la descarga de moléculas de agua en la fusión en caliente de la pasta de soldadura. Cuando se enfría, la pasta de soldadura fundida en caliente se vuelve sólida, y hay pocas cavidades.
Por supuesto, la adición de nitrógeno a la soldadura por reflujo también tiene sus desventajas, tales como no rentable, aumentar la probabilidad de lápidas, mayor efecto de mecha, etc.
En general, la elección de añadir nitrógeno depende de cada situación y proyecto.
Pruebas e inspección de ensamblaje de PCB
La prueba PCBA se refiere a la prueba de conductividad eléctrica y valor de entrada-salida basada en la placa PCBA con componentes electrónicos.
¿Por qué son necesarias las pruebas de PCBA?
En el diseño de PCB, existe una relación numérica entre los diferentes puntos de prueba, como el voltaje y la corriente. Sin embargo, el flujo del proceso de producción y procesamiento de PCBA es muy complejo, incluyendo muchos procesos importantes, como el proceso de fabricación de PCB, la adquisición de componentes, y la inspección, ensamblaje de parches SMT, prueba de PCBA por inmersión. En el proceso de producción y procesamiento, pueden ocurrir varios problemas debido a un equipo o funcionamiento inadecuado. Por lo tanto, es necesario utilizar un equipo de prueba profesional o un multímetro manual para probar los puntos de prueba, para verificar si la placa PCBA real cumple con los requisitos de diseño y garantizar que cada producto no tendrá problemas de calidad.
Las pruebas de PCBA son un paso clave para garantizar la calidad de la producción y la entrega. El dispositivo de prueba FCT se fabrica de acuerdo con el programa de puntos de prueba y los pasos de prueba diseñados por los clientes y, a continuación, la placa PCBA se coloca en el bastidor de prueba FCT para completar la prueba.
Las pruebas son cruciales para garantizar la entrega de productos de alta calidad a los clientes. Afortunadamente, los ensambladores de circuitos impresos ofrecen múltiples niveles de pruebas e inspección para garantizar la producción y entrega a los clientes de circuitos impresos ensamblados de alta calidad. A pesar de todos los esfuerzos por evitar errores, el ensamblaje de PCB es un proceso complejo y a veces se producen defectos relacionados con diversos problemas, desde la carga incorrecta de componentes hasta fallos en el equipo SMT. A lo largo de todo el proceso de producción se realizan pruebas e inspecciones minuciosas para garantizar que los problemas se detectan en una fase temprana y que la calidad y el rendimiento son elevados.
Breve análisis de tres procesos de estarcido para PCB
1. La pantalla de pasta de soldadura: Como su nombre indica, se utiliza para cepillar la pasta de soldadura. Se cortan agujeros en una lámina de acero correspondientes al pad de soldadura de la placa PCB. A continuación, utilice pasta de soldadura para transferir e imprimir en la placa PCB a través de una plantilla. Cuando se imprime pasta de soldadura, ésta se aplica por encima de la plantilla, mientras que la placa de circuito se coloca por debajo de la plantilla. A continuación, se utiliza un raspador para raspar la pasta de soldadura uniformemente en los orificios del esténcil (cuando se aprieta la pasta de soldadura, fluirá hacia abajo desde los orificios del esténcil y cubrirá la placa de circuito). Pegue los componentes SMD y realice la soldadura por reflujo de manera uniforme. Los componentes enchufables se sueldan manualmente.
2. Plantilla de cola roja: La apertura se realiza entre los dos pads del componente en función del tamaño y tipo de la pieza. Mediante el dispensador de cola (que utiliza aire comprimido para aplicar cola roja al sustrato a través de un cabezal dispensador de cola específico), la cola roja se transfiere a la placa PCB a través de los puntos del esténcil. A continuación, inserte los componentes, espere a que los componentes se adhieran firmemente a la PCB y, a continuación, inserte los componentes enchufables para la soldadura por ola unificada.
3. Esténcil de doble proceso: Cuando una placa PCB necesita ser recubierta con pasta de soldadura y cola roja, es necesario utilizar la plantilla de proceso dual. La plantilla de doble proceso consta de dos plantillas, una plantilla láser ordinaria y una plantilla paso a paso. ¿Cómo determinar si la pasta de soldadura utiliza la plantilla escalonada o la cola roja utiliza la plantilla escalonada? En primer lugar, hay que saber si se aplica primero pasta de soldadura o cola roja. Si la pasta de soldadura se aplica primero, entonces la plantilla de pasta de soldadura se convierte en una plantilla láser normal, y la plantilla de cola roja se convierte en una plantilla por pasos. Si la cola roja se aplica en primer lugar, entonces la plantilla de cola roja se convierte en una plantilla láser normal, y la plantilla de pasta de soldadura se convierte en una plantilla por pasos.
La calidad del esténcil de acero inoxidable para PCB se ve afectada principalmente por los siguientes factores:
1. Proceso de producción
Anteriormente, hemos discutido el proceso de producción de la plantilla de acero inoxidable, y se puede ver que el mejor proceso debe ser el corte por láser de la plantilla de acero inoxidable seguido de un tratamiento de pulido eléctrico. Tanto el grabado químico como el electroconformado tienen procesos propensos a errores, como la fabricación de películas de larga duración, la exposición y el revelado, y el electroconformado también se ve afectado por sustratos desiguales.
2. Materiales utilizados
Incluidos el marco de PCB, la malla metálica, la lámina de acero, el adhesivo, etc. El marco de malla de PCB debe ser capaz de soportar ciertos relés de programa y tener una buena nivelación; Lo mejor es utilizar malla de poliéster, ya que puede mantener una tensión estable durante mucho tiempo; Lo mejor es utilizar láminas de acero de grado 304, y las mates serán más propicias para el laminado de pasta de soldadura (adhesivo) que las de espejo; El adhesivo debe tener suficiente resistencia y ser capaz de soportar cierta corrosión.
3. Diseño de la apertura
La calidad del diseño de la abertura es lo que más influye en la calidad de la pantalla de acero inoxidable para PCB. Como se ha comentado anteriormente, el diseño de las aberturas debe tener en cuenta el proceso de producción, la relación de aspecto, la relación de área, el valor de experiencia, etc.
4. Materiales de producción
La integridad de los materiales de producción también puede afectar a la calidad de la plantilla de acero inoxidable para PCB. Cuanto más completa sea la información, mejor. Al mismo tiempo, cuando coexisten datos, debe quedar claro cuál debe prevalecer. Además, en términos generales, el uso de archivos de datos para crear la plantilla de acero inoxidable puede minimizar los errores tanto como sea posible.
5. Método de uso
Un método de impresión correcto puede mantener la calidad del esténcil de acero inoxidable. Por el contrario, un método de impresión incorrecto, como una presión excesiva o PCB o esténcil de acero inoxidable desigual durante la impresión, puede causar daños en el esténcil de acero inoxidable.
6. Limpieza
La pasta de soldadura (adhesivo) se solidifica con relativa facilidad y, si no se limpia a tiempo, bloqueará la abertura del esténcil de acero inoxidable, dificultando la impresión la próxima vez. Por lo tanto, después de retirar el esténcil de acero inoxidable PCB de la máquina o no imprimir pasta de soldadura en la máquina de impresión durante 1 hora, se debe limpiar de manera oportuna.
7. Almacenamiento
La pantalla de acero inoxidable debe almacenarse en un lugar específico y no debe colocarse al azar para evitar daños accidentales al esténcil de acero inoxidable. Al mismo tiempo, la pantalla de acero inoxidable PCB no debe apilarse, ya que es difícil de manejar y puede doblar el marco de malla.
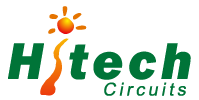
+86-755-29970700 or +86-(0)133 1684 4961
sales@hitechpcb.com; sales15@hitechcircuits.com
2F, Building C, Suojia Technology Park, Hangcheng, Bao’an, Shenzhen, Guangdong, China 518126